Dệt may là một trong những ngành quan trọng đối với nền kinh tế Việt Nam, đóng góp 15% tổng giá trị xuất khẩu và có tốc độ tăng trưởng cao, trung bình đạt trên 12% từ năm 2010 tới 2017. Với hơn 6.000 nhà máy, cung cấp khoảng 3 triệu việc làm trên cả nước, ngành không chỉ quan trọng đối với nền kinh tế mà còn với xã hội Việt Nam.
Tuy nhiên, đây cũng là một ngành có thể gây ra nhiều tác động lên tới môi trường. Quá trình sản xuất của ngành sẽ phải khai thác, sử dụng và xả thải một lượng nước lớn, đồng thời sử dụng nhiều năng lượng cho việc đun nóng và tạo ra hơi nước. Đây chính là những yếu tố tác động lên nguồn nước và góp phần gia tăng khí phát thải nhà kính.
Tác động tới môi trường
Dệt may là một trong những ngành công nghiệp xuất khẩu trọng điểm của cả nước. Năm 2017, ngành đã đạt 31,7 tỷ USD kim ngạch xuất khẩu; năm 2018 dự kiến đạt từ 34 – 34,5 tỷ USD. Mặc dù vậy, đây cũng là một trong những ngành công nghiệp có mức độ phát thải khí nhà kính cao, sau ngành điện và nhiệt, nông nghiệp, giao thông đường bộ và sản xuất dầu khí.
Theo Hiệp hội Dệt May Việt Nam, trung bình mỗi năm, ngành dệt may Việt Nam đang phải chi khoảng 3 tỷ USD cho năng lượng sản xuất, đội giá thành sản xuất lên cao và trở thành một trong những điểm yếu của sản phẩm dệt may Việt Nam. Nguyên nhân chủ yếu là do doanh nghiệp (DN) dệt may trong nước có quy mô nhỏ và vừa, tiềm lực tài chính hạn chế nên vẫn duy trì hệ thống công nghệ sản xuất cũ, tiêu tốn nhiều năng lượng. Cơ cấu sử dụng năng lượng của DN Việt Nam cho thấy chủ yếu là sử dụng năng lượng điện (chiếm 70%), năng lượng hóa thạch (29%) và còn lại là năng lượng sinh khối. Quy trình kiểm soát năng lượng và tiết kiệm năng lượng (TKNL) chưa được các chủ DN quan tâm. Do vậy, cải tiến công nghệ sản xuất theo hướng xanh, sạch, giảm thiểu sử dụng năng lượng là giải pháp cần thiết để tăng năng lực cạnh tranh.
Không chỉ sử dụng nhiều năng lượng, ngành dệt may còn gây ô nhiễm nguồn nước do sử dụng chất hóa học độc hại. Để tạo ra các sản phẩm thời trang, nhiều DN đã đầu tư vào các nhà máy dệt, nhuộm. Các nhà máy dệt, nhuộm sử dụng rất nhiều loại hóa chất như axit, dung môi hữu cơ kiềm tính, thuốc nhuộm và chất màu, các hoạt chất bề mặt. Theo nghiên cứu, trong nước thải dệt nhuộm có cả những chất dễ phân giải vi sinh như bột sắn dùng hồ sợi dọc và những chất khó phân giải vi sinh như: Polyvinyl axetat, thuốc nhuộm phân tán, thuốc nhuộm hoạt tính và các chất dùng tẩy trắng vải. Với các loại vải càng sử dụng nhiều xơ sợi tổng hợp như polyester thì càng dùng nhiều thuốc nhộm và các chất hỗ trợ gây khó hoặc không phân giải vi sinh, dẫn tới lượng chất gây ô nhiễm môi trường trong nước thải càng cao.
Những cơ hội và thách thức trong tiến trình hội nhập
Việt Nam ngày càng hội nhập sâu vào thế giới qua các Hiệp định thương mại tự do (FTA) thế hệ mới như Hiệp định Đối tác toàn diện và Tiến bộ xuyên Thái Bình Dương (CPTPP), các hiệp định thương mại tự do song phương. Dòng vốn FDI được dự báo là sẽ tiếp tục gia tăng mạnh mẽ và ngành may mặc sẽ là một trong những ngành được hưởng lợi. Các hiệp định thương mại tự do thế hệ mới chuẩn bị có hiệu lực như CPTPP hay Hiệp định thương mại tự do Việt Nam – EU đều có quy định về cam kết BVMT, phát thải các bon thấp. Đây vừa là thách thức, vừa là cơ hội, để DN hướng đến đầu tư công nghệ sản xuất hiện đại, sản xuất sạch hơn, tăng tính cạnh tranh của sản phẩm khi xuất khẩu, tăng uy tín thương hiệu đối với người tiêu dùng trong nước.
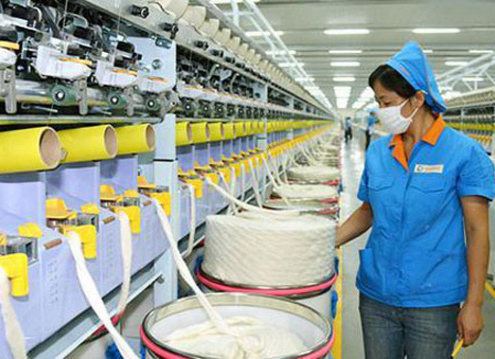
Cải tiến công nghệ trong sản xuất đáp ứng yêu cầu về tiết kiệm năng lượng.
Dệt may Việt Nam đang xuất khẩu sang 4 thị trường lớn là: Mỹ, EU, Nhật Bản, Hàn Quốc và bắt đầu đẩy mạnh hàng hóa vào thị trường mới như Trung Quốc hay Nga. Từ tháng 3/2018, Việt Nam gia nhập CPTPP, mở ra cơ hội để tăng cường xuất khẩu vào những thị trường phi truyền thống như Canada và Ôxtrâylia. Tuy nhiên, sản phẩm dệt may Việt Nam đang chịu áp lực cạnh tranh lớn về giá thành, chi phí sản xuất và tiêu chuẩn an toàn môi trường, sức khỏe người lao động.
TKNL, giảm phát thải đang được coi là hàng rào thương mại lớn của ngành dệt may Việt Nam khi thâm nhập thị trường quốc tế. Hiện nay, một số thị trường lớn như: Mỹ, Liên minh châu Âu đang có quy định về dán nhãn các bon, trong đó, yêu cầu các nhà nhập khẩu phải đáp ứng yêu cầu về mức độ phát thải các bon trên dây chuyền công nghệ sản xuất ra sản phẩm dệt may. Các nghiên cứu cho thấy, ngành dệt may đang chiếm 11% tổng nhu cầu năng lượng trong các ngành kinh tế công nghiệp và phát thải khoảng 5 triệu tấn CO2. Công nghiệp dệt may của Việt Nam vẫn nằm trong nhóm nước có cường độ sử dụng năng lượng lớn nhất thế giới, bởi theo tính toán, cứ 1 đồng sản xuất phải mất 1 đồng cho chi phí năng lượng. Có đến gần 200 DN dệt may thuộc diện DN phát thải trọng điểm (tiêu thụ 1.000 tấn CO2 quy đổi). Hiện nay, đa số DN dệt may đã tiếp nhận yêu cầu dán nhãn các bon trên sản phẩm từ nhà nhập khẩu. Bên cạnh đó, nhiều thương hiệu lớn trên thế giới cũng bắt đầu ưu tiên lựa chọn những đối tác DN thực hiện tốt trách nhiệm xã hội, giảm thiểu ô nhiễm môi trường.
Để chủ động ứng phó rào cản kỹ thật ngày càng nghiêm ngặt, Nhà nước cần tạo điều kiện cho DN phối hợp với các nhà khoa học, tổ chức tín dụng để tiếp cận nguồn vốn, khoa học công nghệ về tiết kiệm điện năng; nhân rộng những mô hình TKNL hiệu quả. Các Bộ, ngành liên quan cần thiết phải xây dựng quy định tiêu chuẩn năng lượng tối thiểu cho từng lĩnh vực; hình thành tín chỉ thương mại về các bon; thị trường mua bán tín chỉ các bon; tiêu chuẩn hiệu suất… Đối với các DN cần phải thay đổi tư duy về TKNL trong giảm chi phí và hạ giá thành sản xuất, chủ động tiếp cận chính sách và các chương trình hỗ trợ phát thải thấp. Về lâu dài, cần có cơ chế hoạt động minh bạch cho các công ty dịch vụ năng lượng, công ty tìm kiếm giải pháp tài chính hỗ trợ DN triển khai giải pháp TKNL, từng bước hình thành quỹ quay vòng vốn cho DN.
Xanh hóa ngành dệt may
Trong thời gian qua, Hiệp hội Dệt May Việt Nam phối hợp với WWF – Tổ chức Quốc tế về Bảo vệ Thiên nhiên triển khai một Dự án “Xanh hóa ngành dệt may Việt Nam thông qua cải thiện quản lý nước và năng lượng bền vững” nhằm thúc đẩy quản lý lưu vực sông tốt hơn, góp phần cải thiện chất lượng nguồn nước và sử dụng năng lượng bền vững. Dự án này là một phần của dự án “Thúc đẩy giảm thiểu tác động thông qua chuỗi cung ứng dệt may”, được tài trợ bởi HSBC, nhằm xanh hóa ngành dệt may tại Trung Quốc, Bangladesh, Ấn Độ và Việt Nam.
Dự án sẽ được triển khai từ năm 2018 tới 2020 với mục tiêu là chuyển đổi ngành dệt may tại Việt Nam thông qua tham gia vào các chính sách quản lý ngành và môi trường để mang lại lợi ích xã hội, kinh tế và bảo tồn cho Việt Nam và toàn bộ khu vực sông Mê Công, nơi tập trung gần 50% nhà máy may mặc của cả nước. Trọng tâm chính của Dự án là cải thiện hiệu suất nước và năng lượng, từ đó giảm thiểu tác động của ngành lên tới môi trường. Dự án sẽ hợp tác với các DN để khuyến khích họ chủ động tham gia hơn vào công tác quản lý sông Mê Công, quy hoạch năng lượng bền vững và tạo cơ hội cho các DN này thảo luận về kế hoạch hành động chung nhằm đầu tư và phát triển ngành dệt may một cách bền vững.
Việt Nam cũng cam kết giảm phát thải nhà kính từ nay đến 2030. Do vậy, xanh hóa thành công ngành may mặc Việt Nam sẽ góp phần vào thực hiện mục tiêu về quản trị nguồn nước và sử dụng năng lượng hiệu quả. Sự ra đời của Dự án vào đúng thời điểm mà ngành công nghiệp dệt may đang cần củng cố hệ thống quản lý, nâng cao các tiêu chuẩn về môi trường và xã hội. Cùng với đó, các DN cũng sẽ phải cải tiến công nghệ sản xuất theo hướng xanh, sạch, giảm thiểu sử dụng năng lượng để phù hợp với môi trường kinh doanh toàn cầu nếu không muốn mất đi khả năng cạnh tranh trên thị trường quốc tế.
Lê Thị Hường – Viện Hàn lâm Khoa học và Công nghệ Việt Nam
(Bài đăng trên Tạp chí Môi trường, số 11/2018)