Doanh nghiệp sản xuất thép trước bài toán chi phí năng lượng
Kết thúc năm 2009, ngành thép được đánh giá là một trong những ngành công nghiệp nặng có mức tăng trưởng cao nhất, sản xuất tăng 25% so với năm 2008 và tiêu thụ tăng 30%. Hiện tại cả nước có trên 65 dự án sản xuất gang thép có công suất từ 100.000 tấn mỗi năm trở lên. Để vận hành, hàng năm mức năng lượng tiêu thụ phục vụ cho ngành thép là con số không nhỏ, gây sức ép lớn đối với phân phối điện.
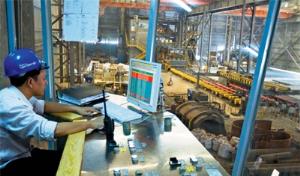
Ảnh minh họa
Số liệu công bố từ Bộ Công Thương cho biết, tính đến ngày 30/8/2009, Việt Nam có 65 dự án sản xuất gang thép có công suất từ 100.000 tấn mỗi năm trở lên. Mặc dù các nhà máy thép mới chỉ sử dụng chưa tới 50% công suất thiết kế nhưng hằng năm tiêu thụ khoảng 3,5 tỷ kWh điện. Để đáp ứng nhu cầu đó ngành điện đã phải đầu tư khoảng 35.500 tỷ đồng cho nguồn, trạm, đường dây dẫn điện.
Nguyên nhân chính dẫn đến mức tiêu hao năng lượng lớn trong ngành sản xuất thép là công nghệ. Với một số nước tiên tiến như Nhật Bản, điện năng tiêu thụ cho 1 tấn phôi thép thành phẩm chỉ khoảng 350-400 KWh trong khi đó Việt Nam phải cần đến 700 kWh. Nếu không có biện pháp cụ thể giảm chi phí sản xuất mà trước tiên là giảm chi phí năng lượng ngành thép Việt Nam không thể cạnh tranh.Hiện tại, trên cả nước nhiều nhà máy gang thép đã quan tâm và áp dụng công nghệ tiết kiệm năng lượng tuy nhiên với mức vốn đầu tư lớn doanh nghiệp đa phần còn ngần ngại. Mặt khác theo ông Trần Mạnh Hùng, Viện Năng lượng, Bộ Công Thương thì “Việc áp dụng những công nghệ tiên tiến cho các nhà máy thép tại Việt Nam bị hạn chế một phần còn là do các lò gang đều có công suất nhỏ hơn 300 tấn. Bên cạnh đó, các nhà máy cán thép có công suất thấp và sử dụng thiết bị lạc hậu mức tiêu hao chênh lệch 30% so với những nhà máy hiện đại.
Nỗ lực giảm chi phí
Hai năm trở lại đây dưới sức ép giá nguyên liệu, nhiên liệu tăng cao cùng với tình trạng chung của khủng hoảng kinh tế ngành thép Việt Nam không tránh khỏi nhiều khó khăn. Trước tính trạng đó, để tăng sức cạnh tranh các doanh nghiệp bắt đầu quan tâm giảm chi phí sản xuất trong đó có các giải pháp sử dụng hiệu quả năng lượng.Ông Phan Mạnh Hùng, Bí thư Đảng ủy, Phó Giám đốc Nhà máy Gang thép Thái nguyên cho biết “Luyện thép là ngành công nghiệp tiêu tốn khá nhiều điện năng. Bởi vậy, Nhà máy chúng tôi đã giảm tối đa việc tiêu hao điện năng bằng cách hạn chế giờ máy ngừng và thời gian chạy không tải. Nhà máy cũng đã thay thế toàn bộ hệ thống điện chiếu sáng trong sản xuất từ bóng đèn sợi đốt sang bóng đèn compact nhằm tiết kiệm điện.
Bên cạnh đó, Nhà máy đã tiến hành giao khoán định mức về tiêu hao nguyên, nhiên liệu cho các đơn vị sản xuất trực thuộc nhằm kiểm soát mức tiêu thụ. Định kỳ hàng tháng, hàng quý, chúng tôi tổ chức đánh giá, nhận xét và dựa trên cơ sở đó để bình bầu thi đua…”.Năm 2009 Công ty liên doanh sản xuất thép Việt-Úc (Hồng Bàng- Hải Phòng) đã thực hiện thay thế lò nung thép công nghệ Đài Loan với mục đích nâng cao năng suất và giảm tiêu hao năng lượng. Cùng với đó, công ty đã tiến hành nâng cấp phần thu hồi nhiệt, sử dụng máy biến tần, dùng bóng đèn tiết kiệm điện, không cán sản phẩm trong giờ cao điểm để hạn chế tối đa chi phí điện năng sử dụng. Với những giải pháp đó mức tiêu hao năng lượng đã giảm 20% so với trước đây.Ông Nguyễn Quốc Hữu, Phó GĐ, ngoài các biện pháp kỹ thuật công ty cố gắng tận dụng tối đa cơ hội giảm chi phí sản xuất từ những giải pháp như tránh sản xuất giờ cao điểm, đẩy mạnh công tác quản lý, giám sát. Nhờ đó, sản phẩm của thép Việt _Úc luôn có tính cạnh tranh cao, thương hiệu được khẳng định nhờ chiến lược sản xuất luôn song hành với tiêu chí bảo vệ môi trường.
Tại Nhà máy sản xuất Thép Pomina mô hình luyện thép theo công nghệ Consteel và cán thép Siemens-vai đã được đưa vào hoạt động từ tháng11/2009. Với công nghệ này, chi phí điện năng giảm 30%, giúp chi phí sản xuất giảm hơn 10 USD/tấn cùng với đó quá trình sản xuất thép phôi nóng được nạp trực tiếp từ nhà máy luyện, giảm đến 30% chi phí gia nhiệt trong quá trình cán thép thành phẩm.
Ngoài sự nỗ lực chủ động của doanh nghiệp, từ năm 2008, Chương trình mục tiêu quốc gia về sử dụng năng lượng tiết kiệm và hiệu quả (Bộ Công Thương) đã giao cho Viện Khoa học và công nghệ Việt Nam thực hiện nhiệm vụ “Hỗ trợ các doanh nghiệp trọng điểm thuộc ngành công nghiệp luyện kim địa phương thực hiện sử dụng năng lượng tiết kiệm và hiệu quả”. Qua 2 năm triển khai nhiệm vụ đã có 7 doanh nghiệp sản xuất thép được chọn để tiến hành kiểm toán năng lượng, tư vẫn và hỗ trợ thực hiện các giải pháp tiết kiệm năng lượng.
Với các giải pháp nêu ra, đến nay nhiều doanh nghiệp đã mạnh dạn đầu tư thực hiện nâng cấp, cải tiến, hợp lý hóa dây chuyền sản xuất, bước đầu đem lại hiệu quả sử dụng năng lượng đáng kể. Cụ thể, sau khi áp dụng các giải pháp, chỉ tính riêng 4 nhà máy sản xuất sắt thép trên địa bàn tỉnh Bắc Ninh đã tiết kiệm được mỗi năm 133 nghìn KWh điện, 112 tấn than và 81 tấn củi. Bên cạnh việc tiết kiệm năng lượng, các giải pháp này còn góp phần giảm 115 tấn khí CO2 phát thải ra môi trường.
Cần mạnh dạn đầu tư
Những giải pháp đơn giản như cải tạo hệ thống chiếu sáng hay thành lập Nhóm quản lý, theo dõi sử dụng năng lượng doanh nghiệp dễ dàng thực hiện bởi vốn đầu tư thấp. Tuy nhiên, với dây chuyền thiết bị cồng kềnh, để cải tạo yêu cầu doanh nghiệp phải chấp nhận đầu tư cao.Chẳng hạn tại Công ty TNHH Tân Đồng Sơn (Xã Vĩnh Lộc B, Bình Chánh, TP Hồ Chí Minh), qua kiểm toán năng lượng đã tìm ra nhiều cơ hội tiết kiệm năng lượng. Trong số đó, có những giải pháp đòi hỏi mức đầu tư hàng trăm triệu đồng như lắp đặt thiết bị Powerboss cần đầu tư trên 283 triệu đồng, giải pháp giảm tổn thất nhiệt thông qua thay thế lớp vỏ lò nung cần mức đầu tư khoảng 166 triệu đồng.
Còn tại Công ty liên doanh sản xuất thép Việt-Úc, để thực hiện giải pháp lắp đặt bộ tận dụng nhiệt khí thải cho sấy dầu đốt lò doanh nghiệp cần bỏ ra mức đầu tư khoảng 1,5 tỷ đồng.Vẫn biết lợi ích kinh tế mang lại là khả quan song không phải doanh nghiệp nào cũng sẵn sàng bỏ đầu tư. Đó là chưa kể đến những giải pháp công nghệ hiện đại hơn như thay đổi công nghệ nung truyền thống sang công nghệ luyện consteel như nhiều quốc gia đã áp dụng, mức đầu tư còn cao hơn rất nhiều. Ông Trần Mạnh Hùng phân tích, công nghệ luyện consteel cho hiệu quả sử dụng điện năng lớn nhưng cần mức đầu tư khá cao, từ 300 triệu USD cho một lò luyện thép công suất 500.000 tấn/ năm. Công nghệ này hiện vẫn vượt ngoài khả năng tài chính của phần lớn các doanh nghiệp sản xuất thép Việt Nam. Tuy nhiên, theo ông Hùng, mặc dù khó nhưng các doanh nghiệp nên cố gắng đầu tư bởi công nghệ sạch, tiết kiệm năng lượng là việc làm cấp thiết, nhằm giữ vững thị phần trong nước, đồng thời đáp ứng được yếu tố bảo vệ môi trường.
Với sự giúp đỡ, tư vấn của các chuyên gia, về lâu dài doanh nghiệp sẽ thu được lợi ích lớn. Với những dự án đòi hỏi một mức vốn lớn, để hỗ trợ cho DN trong việc TKNL nói chung, công cụ hữu ích là cơ chế phát triển sạch CDM. Đây là cơ chế mềm dẻo duy nhất trong Nghị định thư Kyoto có liên quan tới các nước đang phát triển như Việt Nam. Thông qua cơ chế này, DN Việt Nam có thể nhận vốn và kỹ thuật từ các nước phát triển, kể cả DN nhỏ. Tính đến cuối năm 2009, trên thế giới đã có 1907 dự án được chấp nhận là dự án CDM, trong đó các dự án về năng lượng chiếm phần lớn với 60,4%. Tại Việt Nam, đến nay đã có 15 dự án đăng ký, với tổng lượng giảm phát thải là trên 11 triệu tấn CO2, bao gồm thủy điện nhỏ, thu hồi khí đốt, xử lý chất thải…
Nguồn: vneec.gov.vn